Stepper motor selection needs scientific calculation to choose the right motor, we in the selection in addition to pay attention to the size of the flange, phase number, motor length, shaft length, the number of lines, but also calculate the size of the torque, current, and so on, at the same time to confirm the
matching drive.
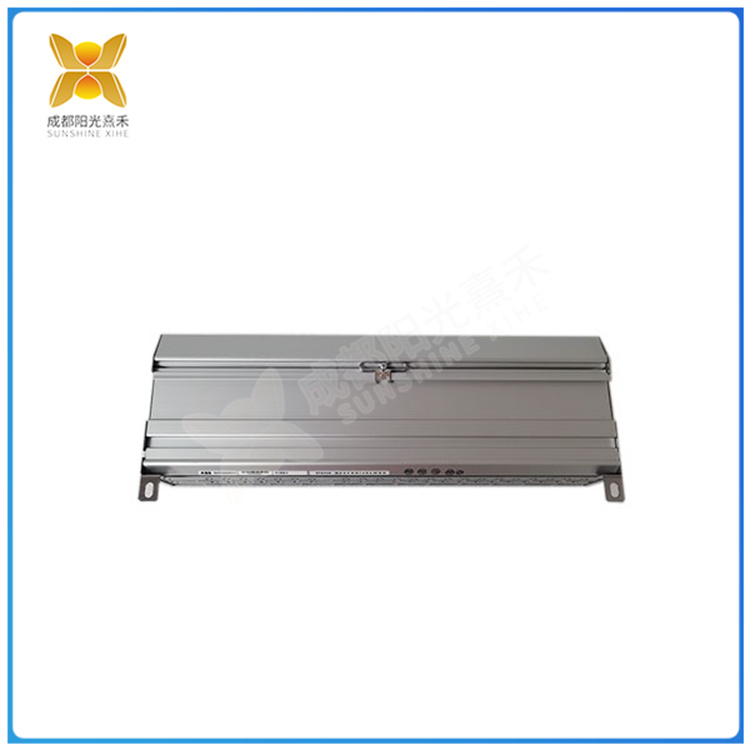
One step motor torque selection
The holding torque of the stepper motor is similar to the "power" of the traditional motor. Of course, there are essential differences. The physical structure of the stepper motor is completely different from the AC and DC motors, and the output power of the motor is variable. Usually according to the size of the torque required (that is, the torque of the object to be driven), to choose which type of motor. For example, the torque is below 0.6N.m, choose 28, 35, 42(the motor body diameter or square, unit: mm); If the torque is above 0.6N.m, 57 motor is more suitable. In the case of a few N.m or greater torque, it is necessary to choose 86, 110, 130 and other specifications of the stepper motor.
Phase selection of a two-step motor
The selection of the phase number of the stepper motor, this content, many customers almost no attention, mostly casually purchased. In fact, different phases of the motor, the working effect is different. The more the number of phases (commonly used are two phases, three phases, five phases), the smaller the step Angle can be, and the vibration at work is relatively small. In most cases, the use of two-phase motors is more. In the high speed and high torque working environment, choose three-phase stepper motor.
Three-step motor speed selection
Special consideration should also be given to the speed of the motor. Because the output torque of the motor is inversely proportional to the speed. That is to say, the stepper motor at a low speed (a few hundred revolutions per minute or lower speed, its output torque is large), the torque in the high-speed rotation state (1000 RPM -9000 RPM) is very small. Of course, some working conditions require high-speed motors, it is necessary to measure the coil resistance, inductance and other indicators of the stepper motor. Choose a motor with a slightly smaller inductance, as a high-speed motor, to obtain a larger output torque. On the contrary, in the case of low speed and large torque, it is necessary to choose an inductance of more than ten or dozens of mH, and the resistance should be larger.
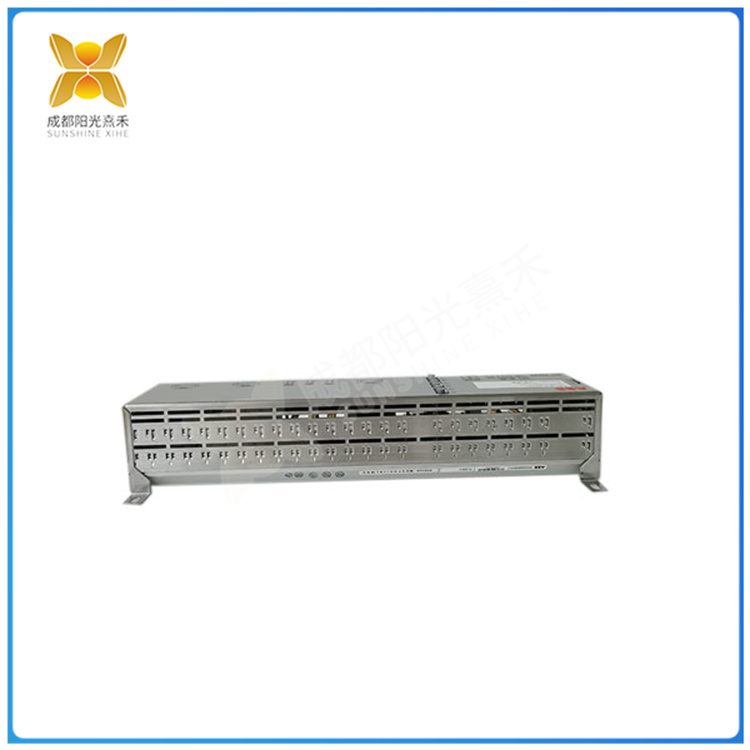
Selection of no-load starting frequency of four-step motor
The no-load starting frequency of the stepper motor is usually called the "no-load frequency". This is a more important indicator for the purchase of motors. If it is required to start and stop frequently in an instant, and the speed is about 1000 RPM (or higher), it is usually necessary to "accelerate start". If you need to start directly to achieve high-speed operation, it is best to choose a reactive or permanent magnet motor. These motors have a relatively high "idle frequency".
For the selection of stepper motor we have the corresponding
strategy and calculation method, you can refer to the calculation method of stepper motor selection for calculation, if you need to fully understand the knowledge before selection, you can call: 0769-23033384, the engineer will help you to do an in-depth understanding!